We’ve all heard the expression, “You can’t compare apples and oranges.” When it comes to the industrial automation industry, the difference between Fieldbus and PLC may be equally confusing.
However, the differences are quite significant and understanding them is crucial for anyone involved in this field.
So, let's dive into the complexities of Fieldbus and PLC, and uncover the distinct roles they play in industrial automation.
Key Takeaways
- Fieldbus enables real-time distributed control and connection of instruments in industrial applications, reducing the need for cables.
- PLCs complement fieldbus technology in industrial automation systems and control various manufacturing processes.
- Fieldbus networks require less cabling compared to traditional 4-20mA installations and offer diagnostics for proactive maintenance.
- Fieldbus networks provide versatile protocol options, enhancing flexibility in system design for system integrators.
Fieldbus Overview
Fieldbus technology enables real-time distributed control and connection of instruments in various industrial applications, significantly reducing the length and number of cables needed for communication. Unlike traditional point-to-point wiring, fieldbuses facilitate a decentralized communication system, allowing for multiple field devices to connect to a single pair of fieldbus wires. This innovation streamlines the automation system, enhancing flexibility and scalability. Fieldbuses, such as PROFIBUS and Foundation Fieldbus, cater to diverse industrial automation needs, offering robust communication protocols for seamless integration with Programmable Logic Controllers (PLCs) and other control devices. These field buses employ various network topologies, including star, tree, and ring, to suit specific application requirements.
Furthermore, fieldbus devices often incorporate microprocessors, enabling sophisticated control schemes and diagnostics at the device level. This empowers the automation system with enhanced intelligence and self-monitoring capabilities, thereby reducing installation and maintenance costs while ensuring high availability and reliability. International standardization efforts, such as the ISA S50.02 standard and IEC 61158, have propelled the evolution of fieldbuses, with ongoing developments focused on safety and real-time Ethernet fieldbuses to meet the ever-growing demands of modern industrial automation systems.
PLC Overview
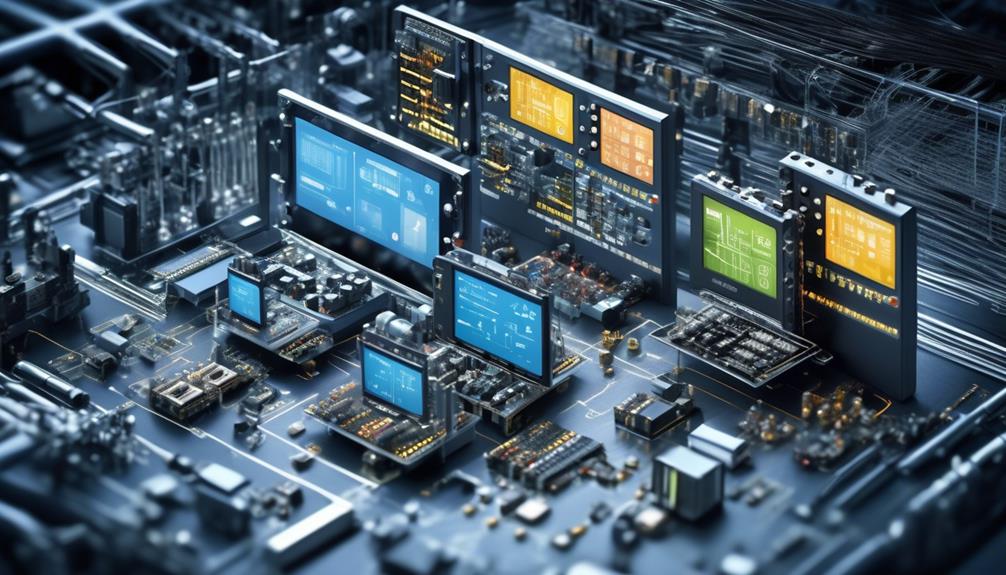
In the realm of industrial automation, Programmable Logic Controllers (PLCs) serve as vital components that complement the capabilities of fieldbus technology, enabling seamless integration and control of various instruments and devices within manufacturing plants.
PLCs are specialized computing devices that are designed to control various manufacturing processes, such as assembly lines and robotic devices. They're programmed using a specific programming language, often relay ladder logic, to execute control functions and operations.
PLCs play a crucial role in real-time distributed control, allowing for precise and efficient management of industrial processes. These devices communicate with fieldbus systems through specific communication protocols, such as Profibus or Ethernet IP, ensuring that data is exchanged effectively between field devices and the PLC.
Furthermore, PLCs are designed to withstand harsh industrial environments and are equipped with numerous inputs and outputs to connect with sensors, actuators, and other industrial equipment. Their flexibility and reliability make them essential for achieving optimal automation and control within manufacturing plants.
Functionality Comparison
Comparing the functionality of Fieldbus and PLC reveals their distinct roles in industrial automation and control systems. Both Fieldbus and PLC play crucial roles in controlling and automating industrial processes within complex automated industrial systems. Here's a detailed comparison of their functionalities:
- Fieldbus is an industrial network system for real-time distributed control, allowing instruments in a manufacturing plant to be connected and reducing the length and number of cables required for communication. On the other hand, PLC is a device connected to the components that perform the work and is traditionally used with analog amplifiers for connections.
- Fieldbus devices often have microprocessors and support control schemes, while PLC operates as a distributed control system with an HMI at the top and a PLC at the bottom.
- Fieldbus networks require less cabling compared to 4-20mA installations and provide diagnostics for proactive maintenance. In contrast, PLC is primarily used for connecting load cells to the components in industrial systems.
- Fieldbus electronics offer a wide range of compatibility with various protocols and installation methods. PLC manages a comprehensive list of fieldbus protocols, including popular ones like Profinet, Ethernet IP, and PROFIBUS, to cater to diverse customer needs.
Applications in Industrial Automation
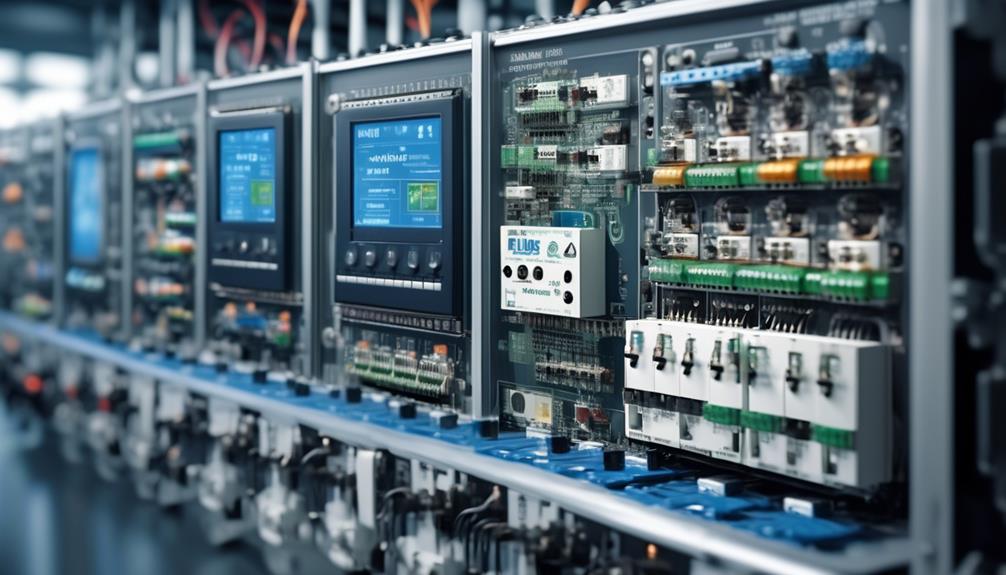
As we explore applications in industrial automation, it becomes evident that the functionality comparison of Fieldbus and PLC highlights their distinct roles within complex industrial systems.
Fieldbus, as an industrial network system, plays a critical role in enabling real-time distributed control and connectivity of instruments in a manufacturing plant. It reduces the need for extensive cabling by supporting various network topologies and incorporating microprocessors in devices. The versatility of various fieldbuses such as PROFIBUS, CAN, and KNX caters to different industrial applications, including industrial automation and process automation.
In the realm of industrial automation, Fieldbus networks offer significant advantages. They facilitate proactive maintenance through diagnostics, reduce cabling requirements, and adhere to specific standards related to the physical media and OSI model layers. Additionally, the incorporation of real-time Ethernet fieldbuses, such as PROFINET IO, adds further depth to the potential applications within distributed control systems.
The standardization of fieldbuses, focusing on commonality and support for safety, underscores their importance in modern industrial automation, where complex systems demand reliable and efficient communication and control.
Advantages and Limitations
Considering the advantages and limitations of fieldbus networks, it becomes evident that their impact on industrial automation is substantial.
- Reduced Installation Costs: Fieldbus networks require less cabling compared to 4-20mA installations, leading to reduced installation costs and complexity, making them an attractive option for industrial applications.
- Improved Maintenance Strategies: Fieldbus networks provide diagnostics for proactive and predictive maintenance, enhancing system reliability and uptime, which is crucial for industrial operations where downtime can result in significant losses.
- Versatile Protocol Options: Fieldbus electronics compatible with various protocols, including popular ones like Profinet, Ethernet IP, and PROFIBUS, offer diverse options for system integrators working on projects with specific protocol requirements, enabling flexibility in system design and implementation.
- Protocol Dominance and Evolving Landscape: The dominance of specific protocols such as Profibus and Ethernet IP, along with the continuous development of new protocols, highlights the dynamic nature of the fieldbus market, necessitating continuous monitoring and adaptation to meet evolving demands and different requirements.
These advantages need to be weighed against limitations such as the potential for compatibility issues when integrating systems using different protocols, and the necessity for continuous monitoring and adaptation to evolving market trends.
Frequently Asked Questions
What Is the Difference Between CAN Bus and Plc?
When it comes to Can bus protocols, they're designed for efficient communication among devices, while PLC programming focuses on controlling machinery and processes.
Can bus technology facilitates streamlined data exchange, whereas PLC control ensures precise automation.
Can bus communication optimizes networked device coordination, while PLC programming manages specific industrial tasks.
What Are the Two Types of Fieldbus?
There are two types of fieldbus systems: digital communication fieldbuses and analog communication fieldbuses.
Some examples of digital communication fieldbuses include Industrial Ethernet, Modbus TCP, and Profibus DP.
On the other hand, analog communication fieldbuses include Foundation Fieldbus.
Both types have distinct advantages and are suitable for specific industrial applications.
It's essential to consider the requirements of the application when choosing between them.
What Is Meant by Fieldbus?
Fieldbus technology revolutionizes industrial automation by enabling efficient data transmission and flexible network architecture.
It utilizes a communication protocol to connect devices, significantly reducing cabling and supporting complex control schemes.
Fieldbus caters to various applications, from process automation to building automation, and incorporates microprocessors in devices.
Its standardization and support for different protocol sets have evolved over the years, making it an essential component in modern manufacturing environments.
What Does a Fieldbus System Do?
Fieldbus communication in industrial automation involves network protocols enabling efficient data transmission among devices. It integrates control systems, reducing cable usage and maintenance costs. With microprocessors, it optimizes distributed control, supporting various topologies. This ensures real-time control and monitoring.
Fieldbus systems streamline operations, enhancing reliability and availability. Plus, they offer proactive maintenance through diagnostic capabilities. Overall, they revolutionize industrial networking for improved performance and cost savings.
Conclusion
In conclusion, Fieldbus and PLC serve different but complementary roles in industrial automation.
Fieldbus focuses on communication and connectivity, while PLC is designed for control and automation.
Both technologies play crucial roles in optimizing industrial processes, reducing the need for extensive cabling, and improving overall efficiency.
Understanding the functionality and purpose of each allows for their effective integration and utilization in manufacturing environments.