So, there has been some conversation about the categorization of CANbus as a fieldbus, and it is a fascinating subject to delve into.
The notion of what constitutes a fieldbus has evolved over time, and CANbus certainly fits the bill in many ways. However, there are nuances and distinctions that warrant a closer examination.
Understanding the technical specifications and functionalities of CANbus in comparison to traditional fieldbuses can shed light on its classification.
Let's unpack this intriguing debate and delve into the specifics of CANbus to determine where it stands in the realm of fieldbus technology.
Key Takeaways
- CANbus is a robust communication protocol widely used in industrial automation.
- CANbus offers a longer transmission distance compared to RS485.
- CANbus supports a higher maximum node access number, providing scalability and flexibility.
- CANbus is immune to noise and has an automatic filter fault function, ensuring reliable data communication.
Canbus Overview
In our overview of Canbus, we'll explore its key features and advantages in the field of industrial communication.
The Controller Area Network (CAN) bus is a robust communication protocol widely used in industrial automation. One of its notable advantages is its ability to transmit data over long distances, with a conventional transmission distance of up to 10 km. This makes it particularly suitable for industrial applications where devices are spread out over a large area.
Additionally, the CAN bus boasts a maximum transmission rate of 1 Mbps, ensuring efficient and rapid communication between nodes. In the context of industrial automation, where real-time data exchange is crucial, this high transmission rate is highly beneficial.
Furthermore, the CAN bus supports a conventional maximum node access number of 110, allowing for the connection of numerous devices within the industrial network. Its immunity to noise and automatic filter fault function further enhance its reliability in industrial environments.
Compared to RS485, the CAN bus structure is simpler and more cost-effective, making it an attractive choice for industrial communication needs.
Characteristics of Fieldbuses
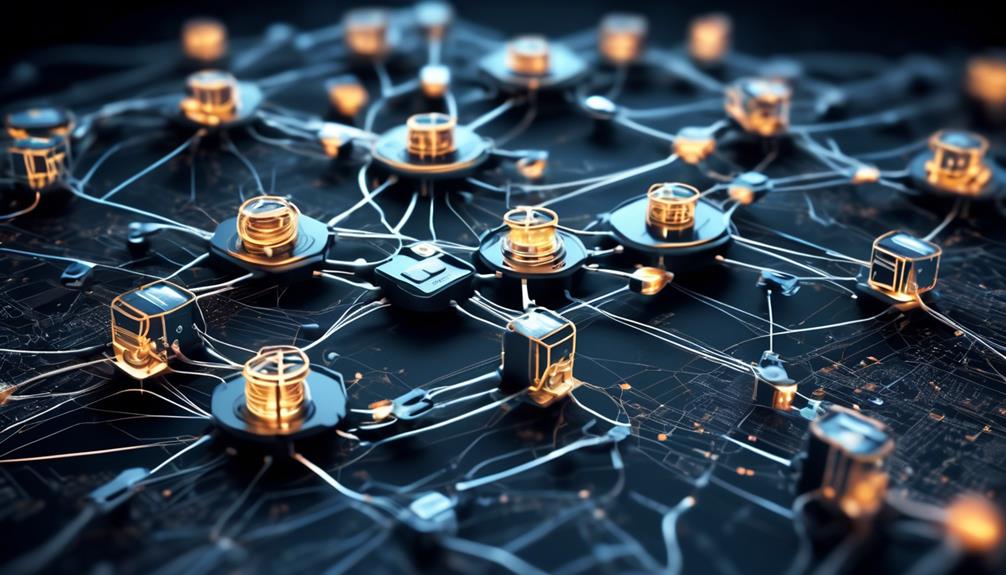
Exploring the characteristics of fieldbuses, we can compare their transmission distances, rates, and node capacities to understand their suitability for industrial communication needs. Fieldbuses like CAN bus and RS485 are integral to industrial communication systems, offering diverse features to meet specific requirements. The table below provides a comparison of key characteristics for these fieldbuses.
Characteristic | CAN Bus | RS485 |
---|---|---|
Transmission Distance | Up to 40 km | Up to 1.2 km |
Data Transmission Rate | Up to 1 Mbps | Up to 10 Mbps |
Node Capacities | Thousands of nodes with CANopen or DeviceNet support | Up to 32 nodes |
These fieldbuses, designed for industrial applications, support real-time signal and data transmission in harsh environments. CAN bus, in particular, offers immunity to noise and automatic filter fault functions, ensuring reliable and secure data transmission. When considering factors such as transmission distance, data transmission rate, and the number of nodes, the choice between CAN bus and RS485 should align with the specific industrial communication requirements. With support for various protocols such as Profibus, CANopen, and DeviceNet, fieldbus systems play a crucial role in integrating numerous components within industrial networks.
Canbus Vs. Traditional Fieldbuses
Comparing Canbus to traditional fieldbuses reveals distinct advantages in terms of transmission distance, node access, and immunity to noise.
Firstly, the CAN bus system offers a longer transmission distance compared to RS485, making it suitable for larger industrial settings.
Secondly, it supports a higher maximum node access number, providing scalability and flexibility for expanding networks.
Thirdly, Canbus is immune to noise and incorporates an automatic filter fault function, ensuring reliable data communication in noisy industrial environments.
In contrast, traditional fieldbuses such as PROFIBUS DP and Industrial Ethernet have their own strengths.
PROFIBUS DP, for instance, offers high-speed data transmission and is widely used in manufacturing automation.
Industrial Ethernet, on the other hand, leverages standard Ethernet technology, providing seamless integration with office networks and leveraging the OSI model for efficient data communication.
However, these traditional fieldbuses may not match the transmission distance, node access, and noise immunity capabilities of the CAN bus system.
Understanding Canbus Functionality

Understanding Canbus functionality involves exploring its communication capabilities and immunity to noise, making it a reliable choice for various applications. Canbus, as a type of fieldbus, provides distinct advantages in terms of communication distance, transmission rate, and network size. To better understand its functionality, let's delve into the key features of Canbus in the table below.
Key Feature | Description |
---|---|
Communication Range | Canbus allows for communication over longer distances, up to 10 km, enabling extensive network coverage. |
Transmission Rate | With a maximum transmission rate of 1 Mbps, Canbus ensures efficient data exchange within the network. |
Noise Immunity | Canbus is immune to noise, ensuring reliable data transmission even in challenging electromagnetic environments. |
Network Scalability | It supports a higher maximum node access number compared to RS485, making it suitable for larger networks. |
Cost-effectiveness | Canbus offers a simpler structure and is cost-effective, making it a suitable choice for various applications beyond the automotive industry. |
These features showcase the robust functionality of Canbus, making it an appealing option for diverse industrial and automotive applications. Additionally, understanding Canbus functionality involves considering its bus arbitration and bus cable, which further contribute to its reliability and efficiency in data transmission.
Determining Canbus Classification
Canbus classification is determined based on its implementation in real-time distributed control systems for industrial applications. The classification of Canbus is crucial for understanding its suitability for specific industrial needs. When determining Canbus classification, the following points should be considered:
- Bus Arbitration: Canbus classification relies on its ability to handle bus arbitration efficiently, ensuring that the communication between nodes is coordinated without conflicts or data collisions.
- According to the Producer-Consumer Model: Canbus classification is determined based on how effectively it adheres to the producer-consumer model, where nodes act as either data producers or consumers, ensuring efficient data exchange.
- Rockwell Automation Guidelines: Canbus classification can also be determined according to Rockwell Automation guidelines, which provide insight into the performance and compatibility of Canbus in industrial control systems.
Understanding these key factors is essential for determining the classification of Canbus in the context of real-time distributed control systems for industrial applications. By evaluating its bus arbitration capabilities, adherence to the producer-consumer model, and alignment with industry standards such as those set by Rockwell Automation, the appropriate classification of Canbus can be established for specific industrial control requirements.
Frequently Asked Questions
Is CAN Bus a Fieldbus Protocol?
Yes, CAN Bus is a fieldbus protocol widely used in various applications due to its advantages such as longer transmission distance, higher maximum node access, and immunity to noise.
When comparing CAN Bus to other fieldbus protocols, factors like transmission distance, rate, and the number of nodes in the network should be considered.
CAN Bus protocol involves efficient and reliable communication through event-oriented message transmission, bitwise arbitration, and priority-oriented communication.
What Is an Example of a Fieldbus?
An example of a fieldbus used in industrial automation systems is the CAN Bus. It offers high-speed data transmission, real-time communication, and scalability for a large number of devices in a network.
Its applications span across various industries, such as automotive, medical, and aerospace.
When comparing different fieldbus types, CAN Bus stands out due to its maximum transmission rate of 1 Mbps and the ability to cover distances of up to 10 km.
What Is a CAN Bus System?
We understand Can bus communication as a fieldbus commonly used in industrial automation. Its architecture allows real-time distributed control and communication between devices.
The applications span across sensors, actuators, and controllers. The Can bus system boasts advantages such as a 10 km transmission distance and a 1 Mbps transmission rate.
Troubleshooting is easier due to its immunity to noise and automatic filter fault function. It supports efficient integration of a large number of devices into a network.
What Are the Devices in Fieldbus?
Fieldbus devices encompass a wide range of industrial instruments, including sensors, actuators, and controllers, designed to communicate using various communication protocols. These devices are integrated into network topology to enable efficient data transmission in industrial applications.
Fieldbus supports seamless device integration and real-time data exchange, enhancing system performance. These technologies are vital in industrial automation, ensuring reliable and robust operation in harsh environments.
Conclusion
In conclusion, CANbus isn't just a fieldbus, it's the superhighway of industrial automation communication. With its high-speed data transmission, real-time communication, and cost-effective scalability, CANbus stands out as the ultimate choice for complex automation systems.
It's like the central nervous system of a factory, allowing all devices to seamlessly communicate and work together, ensuring smooth and efficient operation.
CANbus is the powerhouse of industrial communication, driving the future of automation.